Stainless steel couplings are a critical component across various industries, known for their durability, resilience, and capability to withstand harsh environments. These versatile connectors are pivotal in ensuring the seamless and leak-proof joining of pipes, tubes, and other cylindrical structures, making them indispensable in plumbing, automotive, marine, and industrial applications.
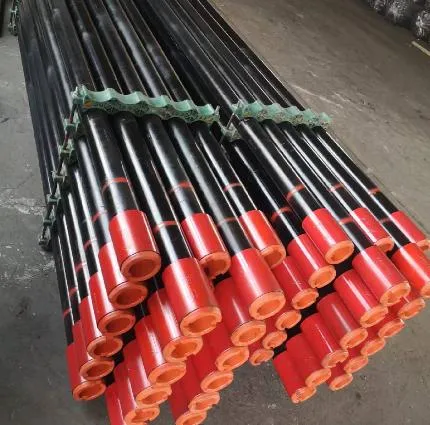
Understanding the specific applications and types of stainless steel couplings can significantly enhance operations by providing longevity and reliability in connections. Their composition, generally consisting of chromium, nickel, and molybdenum, offers exceptional corrosion resistance, which is particularly crucial in environments exposed to moisture, chemicals, or temperature fluctuations.
Stainless steel couplings come in several different types, each tailored to specific needs. The most commonly used are threaded couplings, which are essential in settings where removable or temporary joints are required. Their threaded design ensures a secure fit, eliminating the risk of leakage. In contrast, grooved couplings offer a quick and efficient method for connecting pipes, often used in large scale applications due to their ease of assembly and ability to handle high-pressure systems.
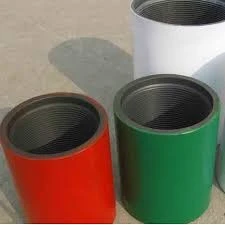
The clamping mechanism in stainless steel couplings also plays a significant role in their functionality. Single-bolt and double-bolt clamps are prevalent, allowing for a tight seal that can accommodate intense pressures and vibrations, essential in mechanical and automotive engineering. Furthermore, quick-connect couplings allow for swift assembly and disassembly, facilitating maintenance and reducing downtime, a critical advantage in manufacturing and emergency repairs.
Efficiency and performance in using stainless steel couplings can be significantly improved by considering factors such as pressure ratings, temperature tolerance, and the specific grade of stainless steel. Grades like 304 and 316 are widely utilized, with 316 offering superior corrosion resistance due to its higher molybdenum content, making it ideally suited for marine and chemical processing applications.
Real-world experience highlights the cost-efficiency and low maintenance requirements of stainless steel couplings. Their robustness means fewer replacements and repairs over time, which can substantially lower operational costs. In industries where safety and reliability are paramount, such as oil and gas or pharmaceuticals, the integrity stainless steel couplings offer is unmatched.
stainless steel coupling
Moreover, their compliance with international standards such as ANSI, ISO, and ASME ensures that they are manufactured to deliver optimal performance. This adherence to standards is crucial for engineers and designers who rely on precise specifications to maintain operational excellence and safety.
Expertise in selecting the right coupling involves an understanding of the specific environmental conditions and mechanical demands. For instance, in food and beverage processing, where sanitary conditions are imperative, stainless steel couplings with polished finishes are often mandated to prevent bacterial growth and ensure hygienic conditions.
The authority in adopting stainless steel couplings also extends to sustainability considerations. As industries push towards greener operations, the long lifespan and recyclability of stainless steel make it an environmentally conscious choice, aligning with global sustainability goals.
Trustworthiness in stainless steel couplings is reinforced by their proven track record and widespread adoption in critical infrastructures. Companies invested in long-term reliability and performance consistently choose stainless steel for its proven ability to perform under duress.
In summary, stainless steel couplings offer an unparalleled combination of strength, reliability, and versatility. Their diverse applications, coupled with their compliance with international standards, make them a cornerstone in industrial and commercial settings. As industries evolve, the innovation and adaptability of these couplings will continue to support efficient, safe, and environmentally sustainable operations worldwide.