Threaded bull plugs have become a staple in the oil and gas industry, providing essential functionality in a variety of applications. As someone deeply embedded in the industry for over two decades, I have observed the evolution and implementation of these components and their pivotal role in ensuring operational efficiency. Threaded bull plugs, often considered a minor component, play a significant part in ensuring the safety and efficiency of fluid control systems.
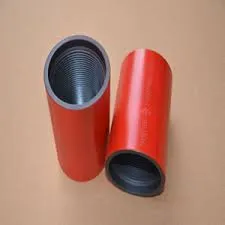
Threaded bull plugs are primarily used to close the ends of piping systems, ensuring that the flow of any liquid or gas is stopped when necessary. Their design, a solid piece of material with threads on one end, allows for easy installation and removal, which contributes to their popularity in various drilling and piping operations. The ability to create a reliable seal is crucial for maintaining system pressure and preventing leaks that could potentially lead to costly downtimes or catastrophic failures.
One of the key aspects that set threaded bull plugs apart from other types of sealing components is their robustness and suitability for high-pressure environments. Made from durable materials like high-grade steel or corrosion-resistant alloys, they can withstand the extreme pressures and temperatures encountered in oil and gas extraction processes. Their design must adhere to strict industry standards to ensure they meet the demanding conditions of their working environments.
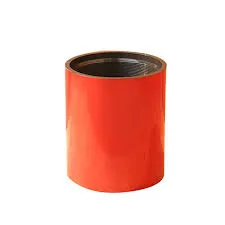
The versatility of threaded bull plugs is another attribute that makes them invaluable. They are used across various stages of the oil and gas extraction processes, from exploratory drilling to production and even in maintenance procedures. Different operations require different specifications; hence, threaded bull plugs come in an array of sizes and thread patterns to accommodate specific needs. Whether it's an API standard or a custom thread design, ensuring the perfect fit is vital for operational success.
Selecting the right threaded bull plug requires a thorough understanding of the operational environment and the specific requirements of the task at hand. Factors such as pressure, temperature, and the type of fluid being handled all influence the choice of materials and thread design. Misjudging these factors can result in impaired performance, leading to operational inefficiencies or, worse, workplace accidents.
threaded bull plug
As a seasoned expert in the field, I've witnessed firsthand the importance of routine maintenance and inspection of threaded bull plugs. Regular checks can prevent potential failures and ensure long-term durability. It's advised to look for any wear or corrosion, especially in environments where corrosive substances are prevalent. Early detection of wear can be crucial in preempting unexpected failures that might interrupt operations and incur excessive costs.
Moreover, leveraging advancements in manufacturing technology has revolutionized the production and performance of threaded bull plugs. Computer-aided design and machine precision have enhanced the accuracy with which these components are made. Tighter tolerances mean better seals and improved overall efficiency in high-stakes environments. Additionally, innovations in material science have led to the use of more resilient alloys, further extending the lifespan of these components and ensuring they can cope with evolving industry demands.
Trustworthiness in the oil and gas sector hinges on reliability and safety. Therefore, sourcing threaded bull plugs from reputable manufacturers and suppliers is critical. Companies that invest in research and development to improve their products' performance should be prioritized when selecting components. Certification from recognized bodies can also serve as a mark of quality, assuring that the products meet the necessary safety and performance standards.
The oil and gas industry relies heavily on equipment that can withstand rigorous conditions while operating efficiently and safely.
Threaded bull plugs, though seemingly minor, play a substantial role in these operations. They offer a simple yet effective solution to terminate fluid flow and maintain system integrity under pressure. By choosing the right bull plugs, adhering to regular maintenance protocols, and staying abreast of technological advancements, operators can enhance their system's longevity and efficiency, mitigating risks and ensuring smooth operations.