The Significance of Coupling for Tubing in Industrial Applications
Coupling for tubing, an essential component in various industrial systems, plays a pivotal role in ensuring the efficient and safe transfer of fluids or gases. It is a mechanical device designed to join two lengths of tubing together, allowing for secure connections that can withstand harsh conditions and demanding applications.
Tubing couplings are available in diverse materials, such as stainless steel, brass, aluminum, and plastic, each chosen based on the specific requirements of the system. The choice of material is crucial, as it directly influences the coupling's durability, resistance to corrosion, and compatibility with the fluid or gas being transported.
One of the primary advantages of tubing couplings is their versatility. They can be used in a wide range of industries, from oil and gas exploration to pharmaceuticals, chemical processing, and even food and beverage manufacturing. In the oil and gas industry, for instance, robust and high-pressure resistant couplings are vital for drilling operations, ensuring the safe transport of hydrocarbons through miles of tubing.
The design of a coupling for tubing can vary greatly, ranging from simple slip-on connectors to more complex threaded or compression fittings. Each design has its unique benefits. For example, quick-release couplings allow for rapid connection and disconnection, which is beneficial in applications where frequent maintenance or changes are required. On the other hand, threaded couplings provide a more permanent seal, ideal for situations where leakage cannot be tolerated On the other hand, threaded couplings provide a more permanent seal, ideal for situations where leakage cannot be tolerated
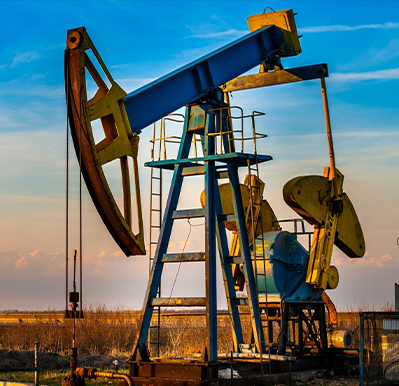
On the other hand, threaded couplings provide a more permanent seal, ideal for situations where leakage cannot be tolerated On the other hand, threaded couplings provide a more permanent seal, ideal for situations where leakage cannot be tolerated
coupling for tubing.
The coupling's sealing mechanism is another critical aspect. O-rings, gaskets, or metal-to-metal seals are commonly used, each offering varying levels of leak-proof performance. The right seal choice is essential to prevent fluid loss, maintain system pressure, and ensure environmental safety.
Moreover, the coupling's ability to withstand extreme temperatures, pressures, and vibrations is paramount. This is particularly true in industries like aerospace or automotive, where tubing systems often operate under harsh conditions. Regular inspection and maintenance of tubing couplings are necessary to ensure their continued integrity and prevent potential failures.
In conclusion, the coupling for tubing is more than just a mechanical connector; it is a safeguard against leaks, a facilitator of smooth operations, and a contributor to overall system reliability. Its selection, design, and maintenance should never be overlooked, as it significantly impacts the efficiency, safety, and longevity of any tubing-based system. Whether it's a small-scale laboratory setup or a large-scale industrial operation, the right coupling can make all the difference.