In the world of oil and gas drilling, the terms tubing and casing are integral to understanding the complex architecture that supports successful extraction operations. These components are not just pieces of metal but are critical to maintaining the structure, safety, and efficiency of boreholes. Tubing and casing serve different purposes, but together they ensure the integrity of the well from the surface to the reservoir.
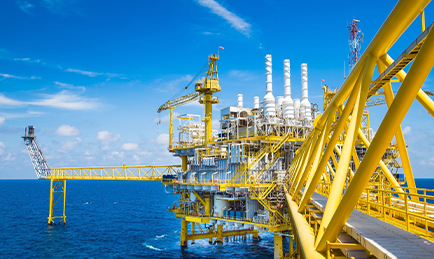
Casing is the first line of defense in wellbore development. It is typically a large diameter pipe that is assembled and inserted into a freshly drilled borehole.
Once in place, cement is pumped around the casing to permanently set it in the hole. This structure serves multiple critical functions It prevents the borehole from caving in, isolates different pressure zones within the borehole to minimize unconventional pressure-related events, and provides a structure from which deeper drilling can occur. Additionally, casing protects the groundwater from contamination by isolating zones of underground water from the drilling fluids and other chemicals.
Tubing, on the other hand, is installed inside the casing and serves as the conduit for the transfer of oil and gas from the bottom of the well to the surface after the well has been completed. Tubing is designed to withstand the pressures and stresses induced by the extraction process. Given the challenging environments in which oil and gas are often found, these tubes must be constructed with precision and resilience to endure significant pressure differentials, corrosion, and other physical demands without failing.
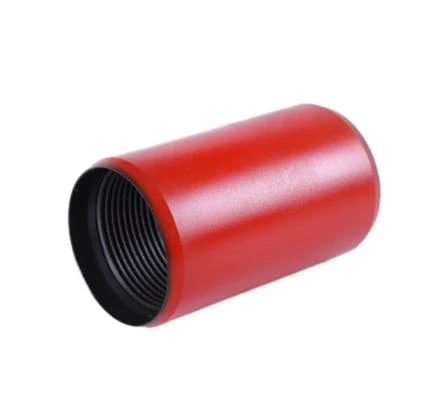
The materials and manufacturing process of tubing and casing are pivotal to their performance. High-strength carbon steel is often used, and in corrosive environments, materials may include stainless steel or other corrosion-resistant alloys. Sophisticated manufacturing processes such as quenching and tempering enhance their mechanical properties, ensuring they can withstand extreme pressures and corrosion from harsh subsurface environments. Non-destructive testing techniques, such as ultrasonic testing and radiographic inspection, are employed to ensure there are no flaws or weaknesses in the materials.
Selection of casing and tubing for specific projects involves a deep understanding of geological and design influences. It requires expertise in interpreting well logs and understanding the pressures the well will encounter over its lifespan. This complexity necessitates the presence of experienced petroleum engineers who possess the technical acumen to make informed decisions on the appropriate size, weight, grade, and material.
tubing and casing
Moreover, the installation process of casing and tubing is a testament to planning and precision. Each joint must be meticulously threaded and sealed to ensure proper alignment and avoid leaks. The intricate process of connecting, running, and cementing casing, along with hanging and testing tubing, demands a multi-disciplinary team working in harmony, highlighting the crucial intersection of human expertise and cutting-edge technology.
Innovation continues to play a pivotal role in enhancing the reliability and efficiency of tubing and casing systems. Advancements in metallurgy, digital monitoring systems, and automated drilling technologies are shaping the future of well integrity. Companies invest heavily in R&D to develop products that can withstand higher temperatures and pressures, deliver better performance, and drive operational efficiencies.
Given the complexity and importance of these components, trustworthiness is paramount. Reputable manufacturers adhere to stringent international standards and regulations, providing certification of compliance to ensure stakeholders that their products meet or exceed industry requirements. This commitment to quality and safety is essential, as failure in any part of the tubular structure can have catastrophic consequences, both financially and environmentally.
The expertise dedicated to selecting, manufacturing, and installing tubing and casing is an art in itself, requiring a blend of experience, technical knowledge, and a commitment to safety. As the energy landscape evolves, the necessity for robust, reliable tubulars becomes even more pronounced, proving that behind every efficient and productive well lies the unseen yet unwavering support of expertly crafted tubing and casing.