Tubing collars, though seemingly mundane components within the vast world of oil and gas production, play a pivotal role in maintaining the structural integrity and functionality of tubular systems. These indispensable devices serve as connectors that effectively join tubing segments, enabling the extraction process to proceed seamlessly. With the oil and gas industry continually evolving and the demands on equipment increasing, understanding the nuances of tubing collars can make a significant difference in operational efficiency and longevity.
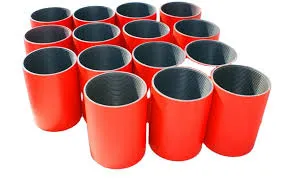
Constructed with high-grade materials to withstand the extreme pressures and temperatures found deep beneath the earth's surface, tubing collars must meet rigorous industry standards. They are often made from carbon steel, stainless steel, or other alloy compositions that offer varying levels of corrosion resistance and strength. The choice of material depends on several factors, including the environment of the well, the types of fluids being transported, and the specific pressures and temperatures involved.
From an expertise perspective, selecting the right tubing collar involves an intricate understanding of not only the materials but also the threading types and specifications. While some applications demand API-standard connections due to their universal acceptance and reliability, other scenarios might benefit from proprietary threading to meet particular operational challenges. Each threading variant, whether it be buttress, extreme line, or premium connections, offers unique benefits that must be evaluated against the project’s demands.
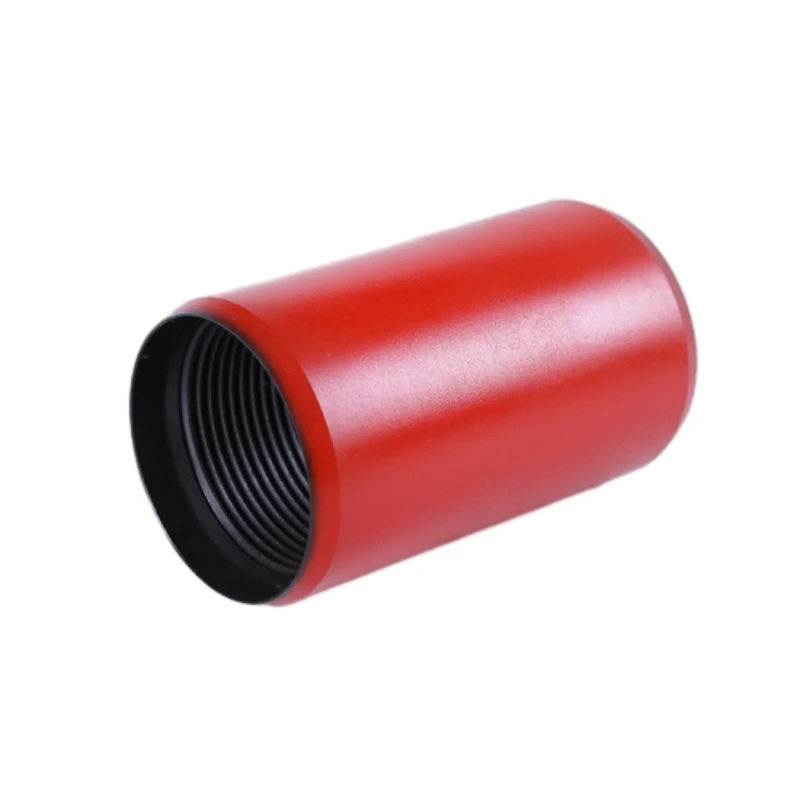
Real-world experience illustrates that incorrect selection or installation of tubing collars can result in significant operational challenges. For instance, misaligned connections or improper torque during installation can compromise the seal, potentially leading to leaks that disrupt production and incur substantial downtime costs.
Therefore, ensuring the precise application of torque and alignment during the installation process cannot be overstressed. Using advanced torque-turn technology and training personnel in best practices has been shown to drastically reduce such occurrences, thus enhancing overall system reliability.
The effective use of tubing collars is also deeply tied to authoritative knowledge within the oil and gas sector. It is essential not only to have hands-on experience but also to stay abreast of technological advancements and regulatory updates. Various governing bodies have laid down strict guidelines emphasizing quality control, encompassing everything from material selection to manufacturing processes. Adhering to these guidelines ensures safety and performance while fortifying the trust stakeholders place in the operation.
tubing collar
Trustworthiness is another crucial factor underpinning the use of tubing collars, predominantly in how they are tested and validated before deployment. Rigorous testing protocols, including non-destructive testing methods such as ultrasonic testing, ensure that each collar meets or exceeds performance expectations. This not only reassures operators of the component's reliability but also safeguards against unforeseen operational failures.
The digital era has transformed how operators manage these components. Advanced software solutions now allow for predictive maintenance and real-time monitoring of tubing collar performance. By integrating such technologies, companies can anticipate potential issues before they manifest, allowing for preemptive measures that significantly mitigate risks.
Moreover, the environmental considerations surrounding tubing collar use are becoming increasingly pertinent. As businesses pledge allegiance to more sustainable practices, the fusion of eco-friendly materials and recycling strategies in manufacturing processes has begun to gain traction. These innovations safeguard the future not just of operations but also of the planet, reinforcing responsible production ideals.
Ultimately, silicon collars manifest more than just the intersection of metal and mechanics; they symbolize the critical importance of collaboration between industry knowledge, technological innovation, and regulatory adherence. For businesses aiming to thrive in the competitive oil and gas landscape, leveraging expertise and authority in the selection and application of tubing collars will be instrumental. Trust, largely accrued through consistent quality and reliability, forms the backbone of lasting success in managing these vital components. By staying informed with the latest in industry advancements and maintaining rigorous testing and installation protocols, operators can ensure that their operations remain robust, efficient, and secure.