In the ever-evolving field of oil and gas exploration, the reliability and efficiency of equipment play a pivotal role in the successful extraction of resources. Amongst the critical components in the drilling process, tubing couplings stand out as essential for maintaining the integrity and flow of fluids within a well. Understanding their function, types, and maintenance is not just recommended but imperative to ensuring seamless operations in challenging environments.
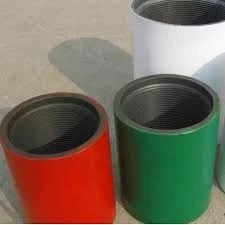
Tubing couplings are designed to connect segments of tubing, providing a secure and leak-proof channel for oil, gas, or water during extraction. These devices must withstand high pressures, temperatures, and corrosive conditions deep underground, making their selection and handling critical to minimizing downtime and maximizing output.
With years of hands-on experience in the field, I have witnessed firsthand the difference high-quality tubing couplings can make. A well-chosen coupling not only supports efficient extraction but can significantly extend the lifespan of tubing strings by offering superior protection against environmental stressors. For instance, couplings made from premium materials like stainless steel or Incoloy alloys, though initially more expensive, prove cost-effective in the long run due to their resistance to wear and corrosion.
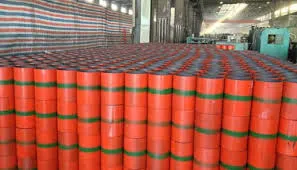
Expertise in selecting and maintaining tubing couplings is central to optimizing their performance. Key factors to consider include material compatibility with the fluid being transported, the expected pressure and temperature conditions, and the specific geology of the drilling site. By thoroughly understanding these variables, operators can make informed choices that enhance both safety and efficiency.
tubing coupling
The credibility of a product in this niche is often gauged by standards and certifications, such as those from the American Petroleum Institute (API). Certified couplings assure compliance with industry benchmarks, thus safeguarding against the risks of mechanical failures or operational inefficiencies. Working with suppliers who adhere to these standards adds another layer of reliability to your operations.
Trust is further built through diligent maintenance practices. Regular inspections and non-destructive testing (NDT) can detect early signs of wear or damage that could lead to catastrophic failures if left unchecked. A predictive maintenance schedule enables operators to pre-emptively replace worn-out components, maintaining continuous operation without unexpected shutdowns.
Lastly, the importance of a comprehensive documentation and data management system cannot be overstated. Detailed records of coupling specifications, installation dates, and maintenance histories are invaluable. They provide the operational insights necessary for long-term planning and efficiency improvements. Implementing an advanced well integrity management system that includes these records can significantly reduce the risk of incidents and the overall cost of operation.
In conclusion, tubing couplings may seem like a modest component in the grand scheme of oil and gas extraction, but their role is fundamental. Mastering their application and maintenance requires a blend of technical knowledge, procedural discipline, and strategic foresight. By prioritizing quality, expertise, and trust in their management, operators not only ensure smooth and efficient oilfield operations but also contribute to the sustainable and responsible extraction of natural resources.