Tubing coupling plays a critical role in the oil and gas industry, serving as a fundamental component that ensures the integrity and efficiency of various piping systems. For industry professionals, understanding the nuances of tubing couplings is paramount to maintaining operations that are both safe and cost-effective.
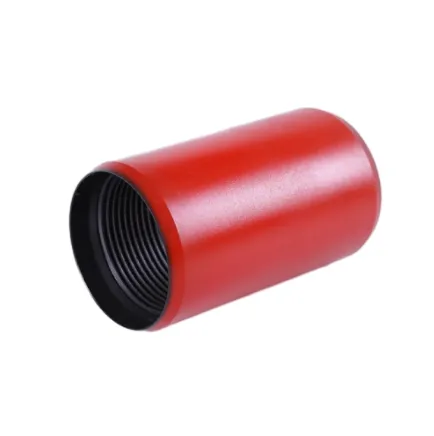
An often-underappreciated aspect of tubing couplings is their design diversity, specifically crafted to cater to different operational needs and environmental conditions. From premium connections to API couplings, each type holds unique specifications to accommodate specific pressure ratings and corrosive environments. In the realm of premium connections, advancements in metallurgy and design have significantly enhanced the sealing capabilities and tensile strength of modern couplings. This improvement is especially pertinent in high-pressure, high-temperature (HPHT) conditions, where traditional couplings may fail.
To truly appreciate the significance of tubing couplings, one must delve into the manufacturing precision that goes into producing these components. The tolerances involved are minuscule, yet critical—often in the order of micrometers—which ensures a snug fit between the coupling and the tubing body. Such precision manufacturing is a testament to the expertise required in coupling production, highlighting how pivotal quality control processes are in the oil and gas sector. By adhering to stringent manufacturing standards, companies can assure that their couplings will perform reliably over extended periods, even in the most challenging environments.
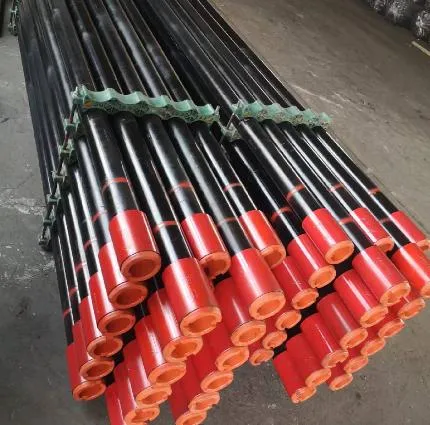
The evolution of tubing couplings also brings forward considerations in material science. The increasing demand for enhanced longevity and resistance in tubing couplings has led to the utilization of alloys like duplex and super duplex stainless steels. These materials are renowned for their superior strength and resistance to chloride-induced stress corrosion cracking, a common issue in offshore operations. The choice of material is critical in prolonging the service life of couplings, which, in turn, reduces the frequency of maintenance interventions and the associated operational downtimes.
tubing coupling
The application of cutting-edge technology in the design and testing phases further bolsters the reliability of tubing couplings. Finite Element Analysis (FEA) and advanced computational simulations now allow for the preemptive identification of potential stress points and failure modes under various loading conditions. Such advancements exemplify the integration of engineering expertise into ensuring coupling performance, enhancing trust in the product's operational viability.
From an operational perspective, the installment process of tubing couplings requires meticulous attention to detail.
Proper torque application is crucial to prevent any compromise in the coupling’s structural integrity. Over-tightening may lead to thread galling, while insufficient torque might result in joint leakage. Field operators, therefore, must be equipped with comprehensive training and guidelines to ensure precision in coupling installation, safeguarding against premature wear and operational failures.
The authoritative nature of industry standards, such as those set by the American Petroleum Institute (API), provides a unified benchmark that assures the reliability of tubing couplings across various applications. These standards not only guide manufacturing practices but also instill confidence among users regarding the product’s trustworthiness and consistency.
In conclusion, the intricate design, precision manufacturing, strict quality standards, and informed material choices collectively underscore the significant role that tubing couplings play in the seamless functioning of oil and gas pipelines. As technological advancements continue to unfold, the expectancy of tubing couplings to adapt and overcome future industry challenges remains a constant pursuit. Their ongoing evolution is a reflection of the industry’s commitment to innovation and resilience, ensuring that these vital components will persist as the backbone of efficient and safe piping systems well into the future.