Well casing couplers play a pivotal role in the oil and gas industry, providing critical support and enhancing the efficiency of wellbore operations. These components, often overlooked by many outside the industry, are essential in maintaining the integrity and robustness of well casings, which are indispensable for the safe and efficient extraction of resources from beneath the earth's surface.
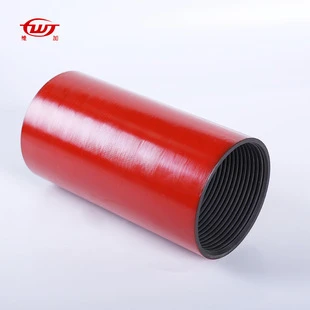
In the world of petroleum engineering, where precision and reliability are non-negotiable, well casing couplers function as the connecting piece that joins sections of casing together. Their fundamental role in providing a secure and leak-proof connection cannot be overstated. It's these attributes that ensure the smooth transmission of extracted materials to the surface, minimizing any operational hiccups that might disrupt production.
One must emphasize the engineering expertise involved in designing and manufacturing well casing couplers. This expertise ensures that these components can withstand the extreme pressures and temperatures encountered deep underground. A coupler's failure could lead to disastrous results, including contamination of groundwater, a blowout, or other costly accidents. Thus, the robust material selection, precision engineering processes, and stringent quality checks underscore the expertise and authority manufacturers hold in this domain.
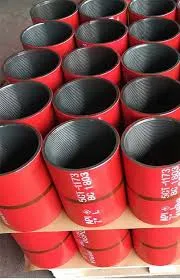
In discussing well casing couplers, it is essential to shed light on the technological advances that continue to shape their development. Modern couplers benefit from enhanced materials such as advanced alloys and composite materials, which bestow increased strength and resistance to corrosion. These improvements result in longer-lasting connections, fewer replacements, and, consequently, significant cost savings in the long-term operation of wells.
well casing coupler
From an operational experience perspective, companies specializing in well casing couplers often provide valuable insights and support to drilling operations. Their involvement often extends beyond mere provision of components to include on-site assistance, consultation during the planning phase, and even post-installation monitoring. This level of service exemplifies the high standards of experience and trustworthiness operators should expect from their suppliers.
Authoritativeness in the well casing coupler market is not just about providing high-quality products; it’s about setting industry standards and contributing to the body of knowledge in the field. Leading manufacturers invest heavily in research and development to stay ahead of emerging drilling technologies and to refine their products continually. Participation in industry forums, contribution to scholarly journals on petroleum engineering, and adherence to international safety and quality standards reinforce a company's authority and reputation.
Trustworthiness is another critical factor operators consider when selecting well casing couplers. Reliability and consistency in performance are paramount, given the potential risks and costs associated with well integrity. Manufacturers that have established a track record of zero-failure incidences and that offer warranties and ironclad guarantees tend to rise to the top in terms of trust. These manufacturers often invite third-party verifications of their products' performance to provide an additional layer of assurance to clients.
In conclusion, the complexity and importance of well casing couplers demand a nuanced understanding of their production, application, and performance. Companies looking to excel in this space must exhibit a blend of innovation, expertise, reliability, and customer-oriented service. For players in the oil and gas industry, selecting high-quality couplers means investing in components that ensure operational continuity, safety, and efficiency, underscoring the fact that attention to these small but mighty components can lead to significant dividends in the overall operational scheme.