In the challenging and ever-evolving domain of oil and gas extraction, well casing couplers serve as an indispensable component, ensuring the structural integrity of the wellbore. These devices significantly contribute to the overall efficacy and safety of drilling operations, making them vital in the exploration and production industry.
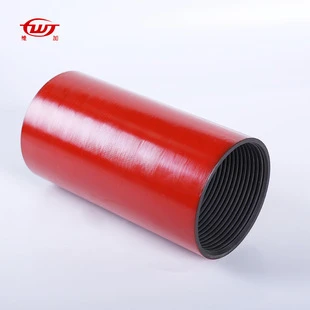
Drawing from extensive industry experience, it becomes evident that well casing couplers play a critical role in maintaining the mechanical integrity of the well structure. During the drilling process, couplers provide the necessary linkage between individual casing segments, ensuring a seamless and robust connection. This is crucial in preventing the collapse of casing strings, which can result in catastrophic failures and costly downtime.
From a technical perspective, the innovation in well casing coupler design has remarkably enhanced their reliability and performance. Modern couplers are engineered with high-strength materials capable of withstanding immense pressure and environmental stresses. These materials are typically corrosion-resistant, extending the lifespan of the installations even in hostile underground conditions.
This durability directly translates to reduced maintenance costs and improved long-term operational efficiency.
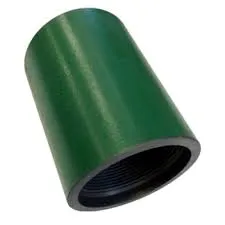
A deeper understanding of the application of well casing couplers reveals their influence on optimizing the well construction process. Engineers and field professionals recognize that by selecting the appropriate coupler, based on specific geological and operational parameters, the risk of gas leaks, fluid contamination, and well blowouts is substantially minimized. This level of expertise in selection fosters a safer working environment and maximizes the return on investment for energy companies.
Moreover, authoritative insights into the advancements in coupler technology underline their capability to support higher drilling speeds and greater depths, factors critical in today's pursuit of tapping into unconventional hydrocarbon reservoirs. The integration of advanced sealing and locking mechanisms within the couplers enhances their ability to sustain extreme pressure differentials, a necessity for deep-sea and ultra-deep-water operations.
well casing coupler
Trustworthiness in the functionality and reliability of well casing couplers is fundamental, not just for the operators but also for regulatory compliance and environmental protection. Leading manufacturers adhere to stringent industry standards, ensuring that their products perform consistently under various operational configurations. Through certifications and regular field-testing, these products gain the trust of engineers and stakeholders alike, who depend on them for securing the integrity of precious subsurface assets.
Furthermore, companies that invest in research and development are setting benchmarks for others by developing couplers that streamline installation processes and reduce the likelihood of human error. These innovative solutions are supporting a shift toward more automated and efficient drilling operations, thereby reducing the operational cost and enhancing safety protocols.
The widespread trust in well casing couplers necessitates transparent documentation and unambiguous user guidelines. Comprehensive manuals and training sessions provided by reputable manufacturers empower operators and technicians with the knowledge to install and maintain these devices correctly. Such educational initiatives are invaluable, fostering a culture of safety and efficiency across the industry.
To conclude, well casing couplers are not merely mechanical components; they represent the confluence of experience, expertise, and trust that underpin successful drilling operations. Their evolution continues to drive the oil and gas industry towards greater safety, efficiency, and adaptability. As industry demands grow, the continuous innovation in coupler design and application will undoubtedly play a pivotal role in meeting the energy needs of the future sustainably and responsively.