Casing and tubing are integral components in the oil and gas extraction industry, each serving a critical role within the drilling operations. While both are types of pipes used in the drilling process, they fulfill distinct functions requiring a clear understanding to enhance safety, efficiency, and cost-effectiveness in projects. This article delves into the key differences between casing and tubing, focusing on experience, expertise, authoritativeness, and trustworthiness to equip industry professionals with comprehensive insights.
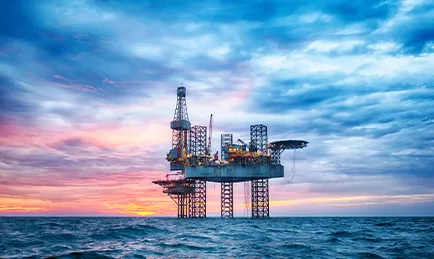
Casing is a large-diameter pipe that is assembled and inserted into a freshly drilled section of a borehole. The primary functions of casing include supporting the wellbore walls, isolating different underground formations to prevent the transfer of fluids between them, stabilizing high-pressure zones, and preventing the contamination of fresh water zones. By lining the well with steel casing, operators provide a stable pathway for the subsequent drilling of deeper sections.
On the other hand, tubing is a smaller-diameter pipe placed inside the casing strings. Its main purpose is to transport hydrocarbons from the wellbore to the surface. Tubing is essential for efficient production operations as it controls the oil flow from the reservoir, minimizes sand entry, and enhances pressure management. Tubing strings are reusable and are regularly taken out and replaced during the lifecycle of a well, which adds an element of operational flexibility.
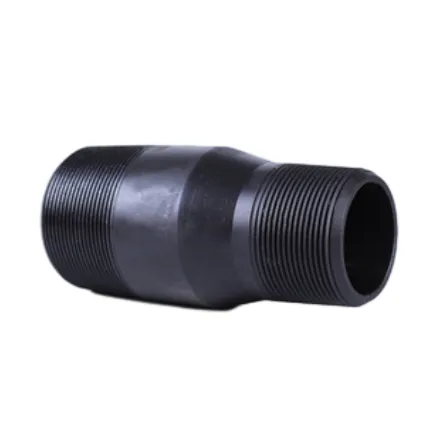
From a materials engineering standpoint, casing is robust and must withstand external pressures from geological formations and internal pressures from drilling fluids. It is typically made from high-strength steel and often augmented with cement to ensure a secure seal and additional strength. Tubing, although also made from strong materials, focuses more on internal pressure containment as well as corrosion resistance due to the direct contact with hydrocarbons and other reservoir fluids. Choices around alloy composition and wall thickness in tubing are influenced by reservoir conditions and fluid characteristics.
In considering the installation processes, casing is installed progressively as drilling progresses. Each time a hole section is drilled, casing is run into the well and cemented in place to secure the formation. Tubing installation occurs after the casing is in place and the well is prepared for production. The variety of tubing connections, such as threaded and coupled joints, influences the speed and reliability of installation processes.
what are the differences between casing and tubing?
Operationally,
the differences manifest in maintenance and monitoring requirements. Casing, once fixed, requires minimal intervention unless specific issues like casing damage or leaks are detected. Tubing, due to its active role in production, experiences wear and tear from the fluid flow and pressure cycles, necessitating regular inspections and sometimes retrieval for maintenance or replacement.
Another crucial difference is the roles these components play in well integrity and safety. The casing design must accommodate potential wellbore instability issues and isolate problematic zones such as water-bearing layers or permeable fronts. Tubing designs emphasize flow efficiency and reservoir management, adapting to changes in production rates and reservoir pressure over time.
When assessing the financial aspects, casing represents a significant initial capital investment due to its critical safety and structural role and is often bespoke to the geological requirements of the well. Tubing requires investment over time as it is subject to wear, and its replacement is a planned component of operational expenditure.
Understanding these distinctions is vital for optimizing drilling operations. Enhanced safety protocols, cost management strategies, and production efficiency all hinge on correctly selecting and using casing and tubing. The industry benefits from a nuanced approach where experience, field conditions, and technological advancements dictate material selection, design parameters, and maintenance regimes.
This segmentation forms the foundation of successful drilling projects, ensuring resource extraction processes are conducted in a safe, efficient, and economically viable manner. Through leveraging expert knowledge, industry professionals can effectively navigate the challenges presented by casing and tubing, achieving both operational excellence and environmental compliance.