Understanding the concept of a bull plug is crucial for professionals in industries such as oil and gas, where precision and safety are paramount. A bull plug is a type of equipment widely utilized for various purposes including sealing and isolation tasks in piping systems. While it may seem straightforward, its role is critically significant, particularly in high-pressure environments.
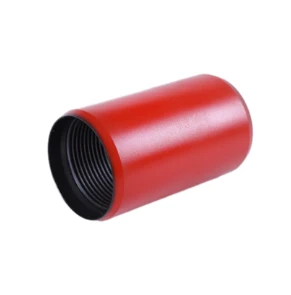
A bull plug serves as a termination point in a piping or tubing system. Typically cylindrical, it is designed to close off the end of a pipe, ensuring that the contents within are safely contained. This is essential in preventing leaks and maintaining the integrity of the piping system. Made from durable materials like carbon steel, stainless steel, or other alloys, bull plugs can withstand high pressure and extreme conditions, making them reliable for a range of applications.
The expertise required to effectively install and maintain these tools includes understanding the specifications and conditions in which the bull plug will be used. For instance, in an oil rig setup, the bull plug must meet precise standards to cope with high-pressure and corrosive environments. Choosing the right material and size is critical; a well-fitted bull plug can enhance the safety and efficiency of the operational setup. Experts often recommend consulting with manufacturers to ensure compatibility with existing systems, taking into account factors such as size, pressure capacity, and material composition.
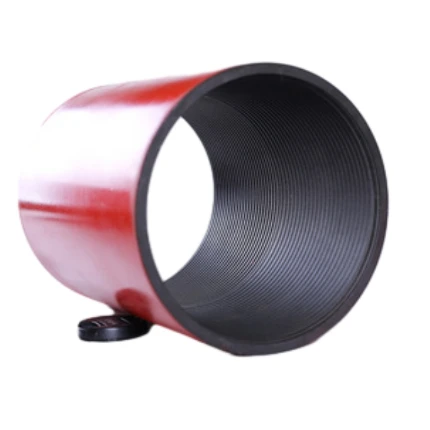
One distinguishing feature of a high-quality bull plug is its versatility. In the field, professionals use these plugs not merely as end caps but also in pressure testing, where the isolation of particular sections of a piping system is necessary to assess its resilience and performance. The expertise needed for pressure testing underscores the requirement for experienced personnel familiar with the mechanics of pressure and potential system vulnerabilities.
what is a bull plug
Authoritative insight on the usage of bull plugs often emphasizes quality control. Certifying bodies and industry standards, such as ASME (American Society of Mechanical Engineers), provide guidelines that manufacturers and users must follow, guaranteeing that the tools meet rigorous safety and performance criteria. A reliable source for acquiring bull plugs is essential as sub-par products can lead to system failures and safety hazards. Therefore, procurement officials and engineers typically work with trusted suppliers who offer certification and adherence to standards.
Trustworthiness in the application of bull plugs also involves regular maintenance checks and replacements. An experienced technician will know to inspect for signs of wear, corrosion, or damage, which could compromise the plug's integrity. This proactive approach minimizes risk and enhances the longevity of the piping system.
In essence, a bull plug’s role extends far beyond a mere closing device. It embodies a critical component in the broader scheme of industrial safety and efficiency. Expert application backed by authoritative advice ensures that operations remain smooth and secure. As industrial demands evolve, maintaining a comprehensive understanding of tools like bull plugs will continue to be indispensable for professionals dedicated to upholding the highest standards of practice.