Bull plugs are an essential component in the oil and gas industry, playing a crucial role in sealing and providing effective pressure control in well operations. Despite their specific utility, choosing the right bull plug with appropriate dimensions is often a nuanced process that requires in-depth understanding and expertise. This article offers a detailed overview, drawing from firsthand industry experiences and specialized knowledge to enhance both your comprehension and trust in the subject matter.
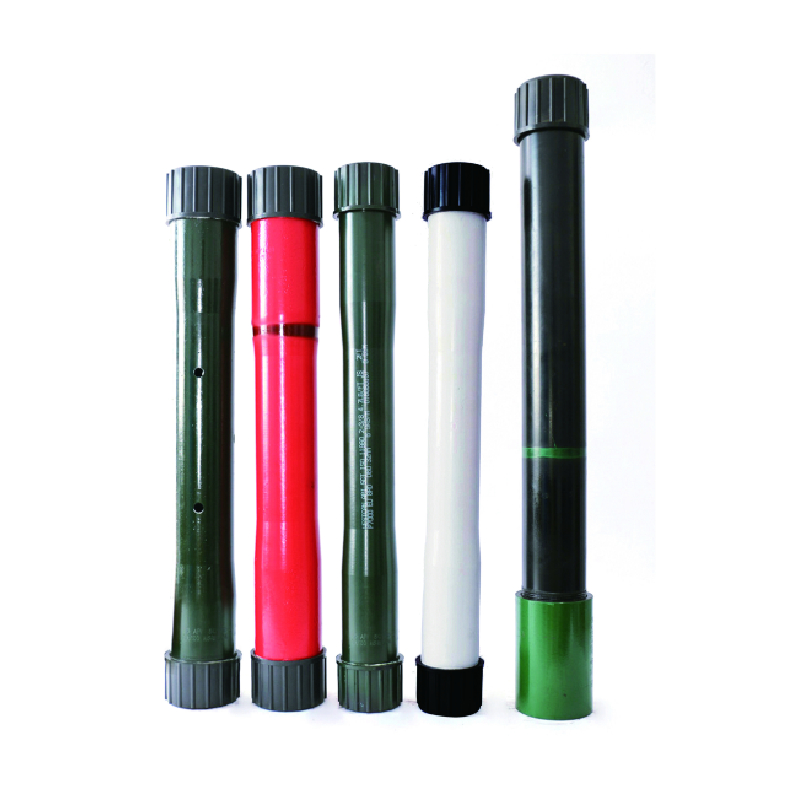
Expert knowledge in selecting bull plugs begins with understanding their construction, which typically includes high-quality steel or stainless steel to withstand extreme conditions. The dimensions of these plugs are paramount. A typical bull plug may range in size from 2 inches to 8 inches in diameter, with variations dependent on the specific requirements of the operation. The careful selection of these dimensions aids in preventing mishaps such as leaks or overpressure situations, thus ensuring the safe and efficient functioning of wells.
Another critical aspect to consider is the pressure rating of the bull plug, which often governs its applicability in various operations. Ratings can generally range from 5000 PSI to upwards of 15,000 PSI, designed to meet different operation specifications. Proper assessment is necessary to ensure compatibility with the operational environment, taking into account both the depth and pressure requirements.
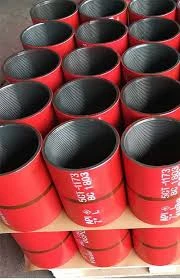
The thread specification of bull plugs further demands attention. Common threading includes API (American Petroleum Institute) standards, such as NPT, LP, or Figure 200. These threading styles are crafted to accommodate seamless integration with different components, reducing the risk of cross-threading and ensuring robust assembly.
The material choice is equally significant. For operations demanding greater resilience against corrosive elements or extreme temperatures, opting for alloy steels such as 4140 or 9CR greatly improves the longevity and reliability of the plug. Having firsthand experience in such environments underscores the necessity of these materials in extending the operational life of a plug, despite their higher upfront costs.
bull plug dimensions
From a professional standpoint, adherence to international and regional standards is a hallmark of quality bull plug manufacturing. Compliance with ISO (International Organization for Standardization) or ASME (American Society of Mechanical Engineers) standards confirms that a bull plug will perform optimally under specified conditions, thus earning both confidence and trustworthiness among engineers and operators alike.
On-site experiences reveal the importance of choosing bull plugs not solely based on theoretical specifications but also on insights gleaned from operational experiences. Factors such as ease of installation, the role of auxiliary tools, and the durability of seals are equally significant in shaping decision-making processes.
Continuous updates on technological advancements are also central elements within the domain of bull plug expertise. Emerging technologies introduce advanced materials and manufacturing techniques that promise enhanced performance and efficiency. Staying informed about these innovations translates into improved decision-making and streamlined operations in real-world applications.
In conclusion, the intricacies attached to selecting the appropriate bull plug dimensions and specifications are vast. Success stems from a deep understanding cultivated through professional experiences and adherence to stringent standards. Trust in the selected equipment is underscored by knowledgeable choices that incorporate both tried-and-true practices and cutting-edge developments, ensuring that each bull plug performs its vital function effectively and reliably in diverse and challenging environments.