In the dynamic world of oil and gas, the bull plug plays a pivotal role, serving as a critical component in the operational integrity and efficiency of drilling operations. Understanding the multifaceted nature of this product not only requires technical knowledge but also practical experience that assures its optimal use.
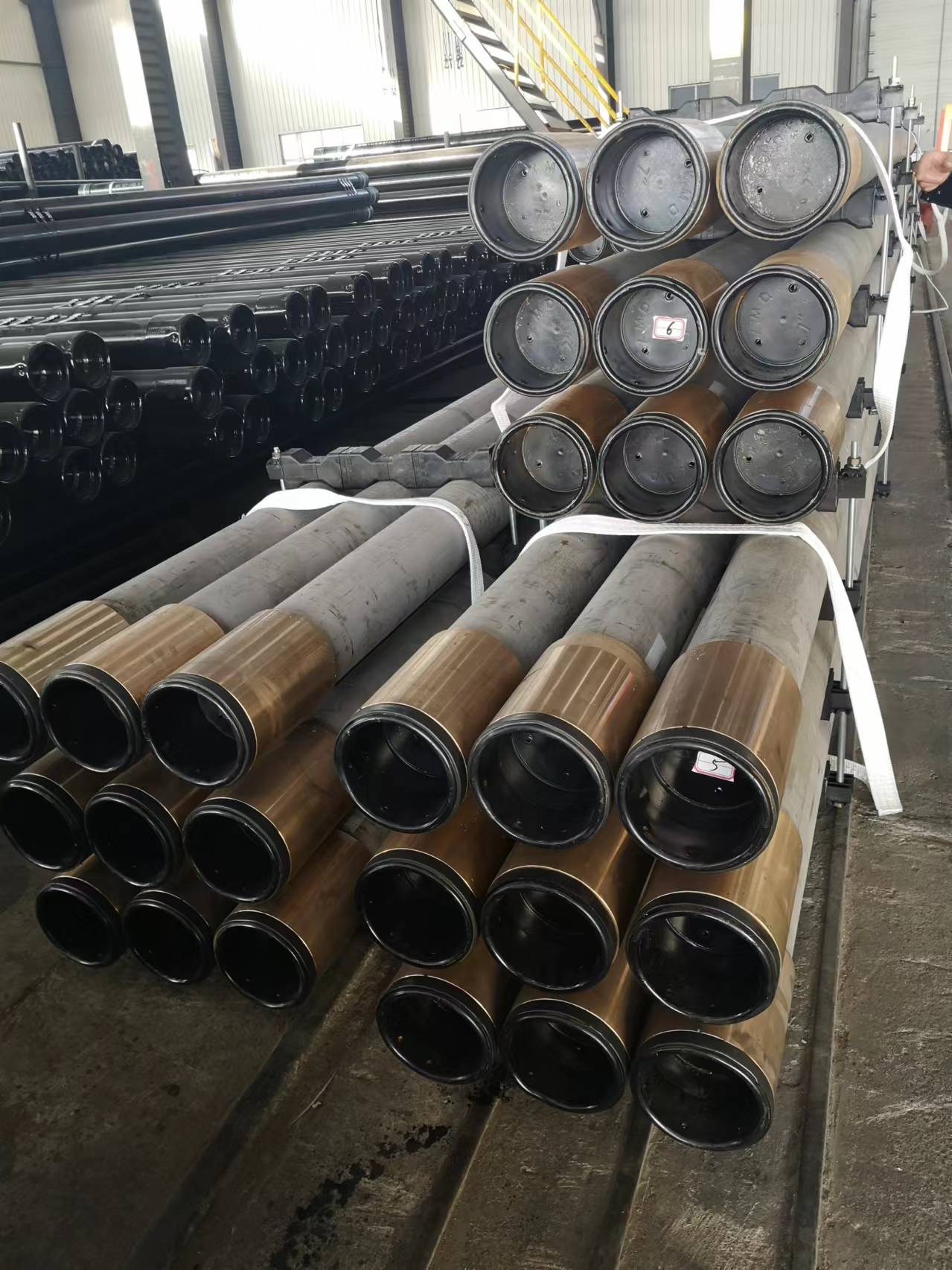
A bull plug is a cylindrical device used to seal off the end of a pipe. It functions as a cap or a plug, providing a pressure-tight barrier. This simplicity belies its significance in preventing leaks and maintaining pressure within the drilling system. Its effectiveness ensures the safety and efficiency of the oil and gas extraction process, making it an indispensable part of an engineer's toolkit.
The manufacturing of bull plugs demands precision and reliability. Fabricated from high-grade materials like stainless steel or carbon steel, each plug must withstand extreme temperatures and pressures typical of drilling environments. This robustness is critical to its role, as failure can result in catastrophic outcomes, including operational downtime and environmental hazards.
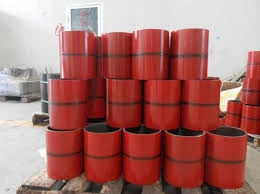
From an expertise standpoint, selecting the appropriate bull plug is imperative. Experts recommend considering factors such as the size and type of the borehole, the material of the pipe, and the specific conditions of the drilling environment. This detailed approach ensures that the chosen bull plug fits seamlessly within the system, providing maximum efficacy.
Field experience further underscores the necessity of bull plugs in maintaining the structural integrity of the drilling setup. Oil and gas veterans recount scenarios where strategically placed bull plugs have averted major accidents by ensuring robust pressure containment. Their firsthand accounts emphasize that while bull plugs are small, their impact is mighty, galvanizing seamless operations in rugged terrains.
bull plug oil and gas
An authoritative understanding of bull plugs also involves recognizing their role in reducing costs. By preventing leaks and ensuring pressure stability, bull plugs contribute significantly to the reduction of material waste and environmental cleanup costs. This cost-benefit analysis is not only persuasive for stakeholders aiming for sustainable practices but also reinforces the strategic value of opting for quality bull plugs.
Trustworthiness in the selection and usage of bull plugs is built on consistent performance and compliance with industry standards. Accredited manufacturers provide detailed certifications and test results, ensuring that their products meet the stringent requirements of the oil and gas sector. These certifications are a fundamental trust builder, guaranteeing that the products will perform as expected under duress.
In recent advancements, innovation in bull plug design and materials has further enhanced their functionality. Some contemporary designs include corrosion-resistant coatings and advanced threading techniques that improve their longevity and adaptability to various pipe systems. These enhancements reflect a commitment to constant improvement, aligning with industry standards and expectations.
Ultimately, the bull plug's contribution to the oil and gas industry extends beyond its size. It embodies a blend of technical precision, material science, and experiential wisdom that together fortify the efficiency and safety of drilling operations. Its continued evolution stands as a testament to the ongoing pursuit of excellence and reliability in the field. For professionals vested in oil and gas extraction, understanding and utilizing bull plugs is not a mere procedural requirement but an essential component of sustainable and innovative practices.