Understanding the differences between casing and tubing in the oil and gas industry is crucial for ensuring operational efficiency and safety. Both casing and tubing are essential components in well construction, but they serve distinctly different purposes. Here, we delve into their unique characteristics, applications, and the vital role they play in oil and gas extraction.
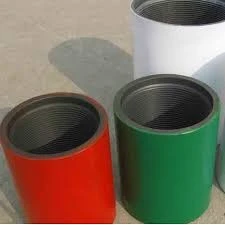
Casing refers to the series of heavy-duty steel pipes that are inserted into a drilled wellbore. Its primary function is to stabilize the well, prevent the collapse of unstable strata, and protect freshwater aquifers from contamination by isolating them from the drilled formation. The casing process typically starts once the well has been drilled to a predetermined depth. After the casing is set, cement is pumped down the casing's interior and back up around the exterior to provide further stability and integrity, forming a seal between the casing and wellbore.
One of the critical differences between casing and tubing lies in their structural design and load-bearing capacity. Casing is robust and thicker, designed to withstand external pressures and the geological forces exerted by the surrounding formations. It is categorized into several types based on its position and function surface casing, intermediate casing, and production casing. Surface casing is the initial layer of protection from the surface into the well. Intermediate casing isolates various zones within the wellbore, while the production casing surrounds the reservoir section, preventing the fluids from entering unwanted zones.
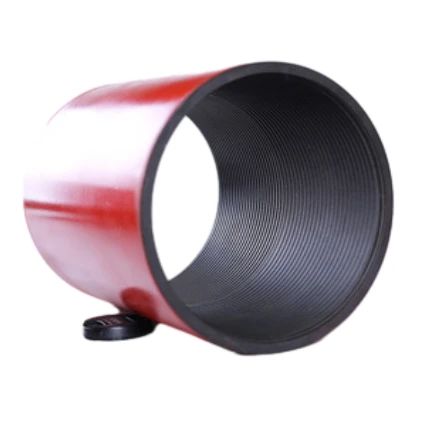
On the other hand, tubing is used inside the casing, its primary purpose being to conduct oil or gas from the production zone to the surface facilities. Tubing is smaller in diameter compared to casing and is designed to withstand internal pressures from the flow of hydrocarbons, rather than external geological forces. Since tubing is integral to the efficient transport of produced fluids, it must be regularly inspected and maintained to ensure optimal flow rates and to avoid any leakage or blockages that could disrupt production.
what is the difference between casing and tubing?
Expertise in selecting the right casing and tubing involves understanding the properties of the formation, the expected pressures, temperatures, and the types of fluids to be conveyed. Material selection for these components must meet industry standards for corrosion resistance and strength. For many professionals in the field, the choice between various casing and tubing materials often hinges on long-term considerations, such as the potential for sour gas presence, which necessitates materials resistant to hydrogen sulfide-induced corrosion.
Authorities in the sector emphasize the importance of testing and quality control to ensure the reliability of casing and tubing installations. Failures in either component can lead to severe environmental and safety hazards, including well blowouts or contamination of water resources. Therefore, strict adherence to industry best practices and regulations is paramount in the design, installation, and maintenance of casing and tubing.
In conclusion, while casing and tubing may seem similar, their roles, design specifications, and operational objectives within a wellbore differ significantly. By ensuring the proper installation and maintenance, operators can safeguard their investments and maintain the productivity and safety of their well operations. This nuanced understanding is crucial not only for engineering success but also for upholding environmental and safety standards in the ever-evolving energy industry.