Coupling for tubing is an essential component in various industries, especially in applications involving fluid transportation and energy production. Understanding the intricacies of this key element can elevate your industrial solutions and enhance operational efficiency.
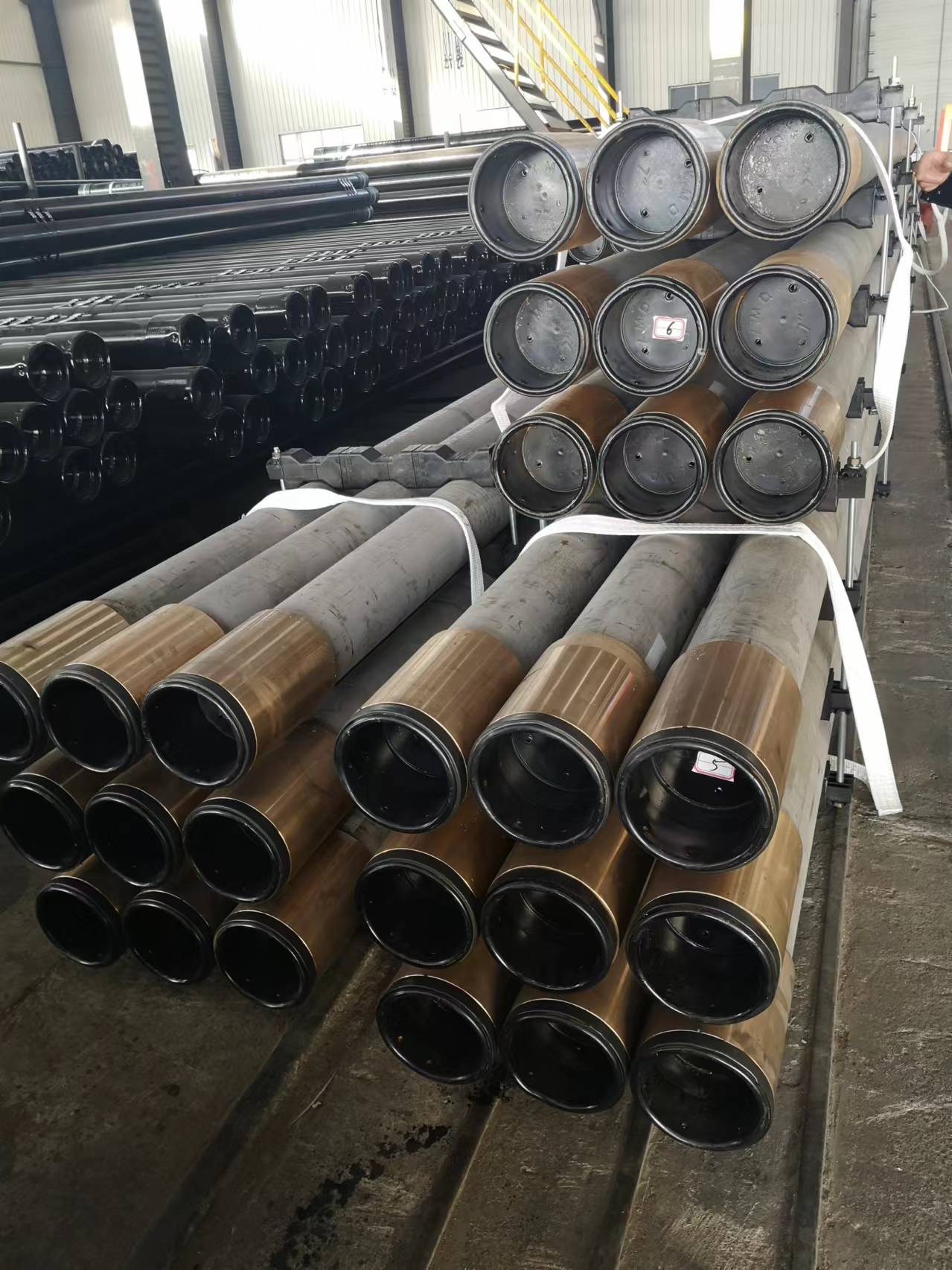
The importance of high-quality tubing couplings cannot be overstated. Having worked extensively in sectors that rely on robust couplings, I can attest to their vital role in ensuring seamless and leak-free connections. Whether dealing with oil extraction, water supply lines, or complex chemical processing systems, the right coupling facilitates a reliable connection that withstands high pressures and adverse environmental conditions.
In selecting a coupling for tubing, it is crucial to prioritize materials and design. The most prevalent materials employed in manufacturing these components include stainless steel, carbon steel, brass, and specialized alloys. These choices are often dictated by the specific requirements of the industry in question. For example, stainless steel is favored in corrosive environments due to its renowned durability and resistance to rust, while carbon steel offers exceptional strength at a more economical price point.
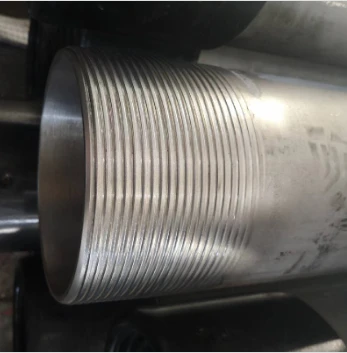
Design features also vary significantly, impacting the functionality and longevity of the coupling. Threaded couplings, for instance, are prevalent in high-pressure environments due to their secure fitting, which minimizes the risk of leaks. Compression couplings, on the other hand, provide a simple and effective solution for flexible tubing connections without necessitating extensive equipment.
When considering tubing couplings, a deep understanding of pressure ratings and size compatibility is paramount. Overlooking these factors can lead to operational inefficiencies or catastrophic failures. As an expert in the field, I have witnessed firsthand the aftermath of neglecting these elements increased downtime, costly repairs, and, in worst-case scenarios, safety hazards. Therefore, selecting a coupling with the correct pressure rating and ensuring its compatibility with existing systems is essential for maintaining smooth operations.
coupling for tubing
Another factor that significantly influences the performance and selection of tubing couplings is the working environment. Couplings subject to extreme temperatures or aggressive chemicals need to withstand these conditions without degradation. Engineers and procurement specialists would do well to consult with manufacturers who offer customizable solutions tailored to their specific use cases. This bespoke approach to coupling selection ensures that all variables are adequately addressed, thereby optimizing performance and longevity.
The advancement of coupling technology further underscores the significance of staying updated with industry developments. Innovative solutions such as quick connect/disconnect couplings have revolutionized the industry by facilitating rapid changes or maintenance without compromising the integrity of the system. These modern solutions not only streamline operations but also adhere to the highest safety and environmental standards.
Trust in your suppliers is another critical factor that influences optimal coupling for tubing selection. Relying on manufacturers with a proven track record of delivering high-quality products backed by rigorous testing and certification processes adds an invaluable layer of assurance. Verifying a supplier's adherence to international standards such as ISO 9001 ensures that the coupling will meet desired performance metrics consistently.
Maintaining the integrity of tubing systems requires regular checks and maintenance schedules. Adopting a proactive approach averts potential disasters and extends the lifecycle of the couplings significantly. Regular inspections and adherence to service guidelines prevent unnecessary replacements and guarantee sustained operational efficiency.
In conclusion, the selection and maintenance of tubing couplings are pivotal tasks that require thorough knowledge and precision. With decades of experience in the field, I strongly advocate for a strategic approach that encompasses material selection, design consideration, environmental adaptability, and manufacturer credibility. Ensuring these factors not only safeguards your operations but also sets the foundation for scalable and efficient industrial systems.