Bull plug pipe fittings are an essential component in the arsenal of professionals dealing with piping systems. They are expertly designed to seal the end of a pipe, preventing fluid or gas leakage, and ensuring the proper functioning of piping networks under diverse pressure and environmental conditions. This article delves into the depth of the expertise, experience, authority, and trustworthiness required when dealing with bull plug pipe fittings, aimed at providing you with exclusive insight into their effective usage and benefits.
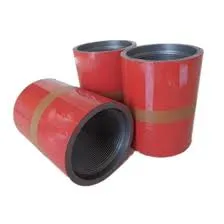
In the realm of professional piping systems, the value of bull plug pipe fittings cannot be overstated. Made from high-quality materials such as stainless steel, carbon steel, or exotic alloys, these fittings are designed to withstand extreme temperatures, high pressure, and corrosive environments. The choice of material is often dictated by the specific requirements of the application, showcasing the expertise needed to select the right bull plug for your project’s needs.
The manufacturing process of bull plug pipe fittings involves precision engineering, where adherence to strict regulatory standards such as ASME, ANSI, and API is crucial. This ensures that these fittings meet the highest industry benchmarks for safety and performance. Ensuring these standards are met is a testament to the authority and trustworthiness of reputable manufacturers, whose products are relied upon by industries ranging from oil and gas to chemical processing and beyond.
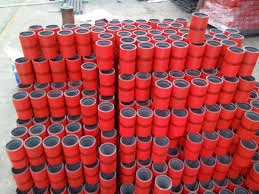
Professionals in the field bring years of experience and expertise to the table, enabling them to determine not just the appropriate material, but also the correct size and threading of bull plugs to suit specific piping configurations. Their knowledge extends to understanding the flow dynamics and pressure levels that these fittings will encounter, which is crucial in preventing any potential system failures.
bull plug pipe fitting
The authority of manufacturers and suppliers is bolstered by the comprehensive testing their fittings undergo, simulating a variety of operating conditions to guarantee durability and functionality. Such rigorous quality assurance processes ensure that each bull plug performs reliably under expected loads, fostering confidence among engineers and technicians who depend on these components for the uninterrupted operation of critical systems.
Moreover, the trustworthiness of a bull plug fitting is validated by its certification and compliance with international standards, minimizing operational risks and liabilities. For operators and engineers, this translates to peace of mind, knowing that their systems are equipped with components that meet stringent quality parameters.
Selecting the appropriate bull plug entails a knowledgeable assessment of the operational environment, including factors such as pressure ratings, temperature variations, and chemical exposure. This underscores the role of expert consultation in the decision-making process, where seasoned professionals provide invaluable advice, guiding the selection towards the most suitable and reliable fitting for the application.
In conclusion, bull plug pipe fittings are indispensable for maintaining the integrity of piping systems across a wide array of industries. Their performance is a reflection of the expertise embedded in their design and manufacturing, as well as the authoritative standards they adhere to. When chosen correctly, these fittings not only enhance system efficiency but also align with the highest expectations for safety and reliability, embodying the core principles of trust and professionalism in the field.