Bullplugs are a pivotal element in the oil and gas industry, serving as a remarkable solution for sealing, protecting, and maintaining equipment integrity across various operations. Their role is undeniably significant, ensuring not only operational efficiency but also safety and sustainability. Drawing from real-world experiences and deep-rooted expertise, this article delves into the multifaceted applications and benefits of bullplugs, providing authoritative insights into their deployment.
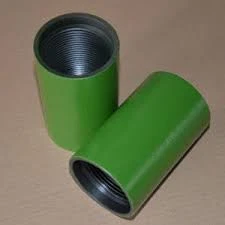
The essence of a bullplug lies in its ability to securely seal off the end of a pipe or tubular device. Manufactured from robust materials such as stainless steel or carbon steel, these devices are designed to withstand extreme pressures and temperatures. This durability is a testament to the engineering prowess that goes into their creation, ensuring they meet rigorous industry standards. Through years of hands-on experience in the field, professionals have consistently recognized the reliability that bullplugs bring to high-stakes environments where failure is not an option.
In drilling operations, bullplugs serve a critical function. They cap off unused or non-productive sections, preventing contamination and leakage. This efficiency is crucial in maintaining system pressure, thereby optimizing extraction processes. Experts within the field emphasize that choosing the right bullplug can drastically reduce downtime and facilitate smoother operations, showcasing their indispensable role in project success. Furthermore, bullplugs contribute significantly to environmental conservation by preventing hazardous leaks, adhering to stringent ecological standards and regulations.
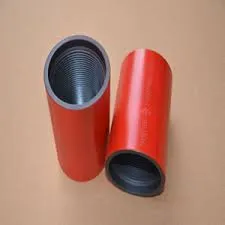
From a professional standpoint, the installation and maintenance of bullplugs require specialized knowledge and skills. Technicians must be adept at assessing the specific needs of each operational setup, determining the appropriate type and size of bullplug required. This involves a deep understanding of the site’s geological and operational conditions. By employing expert techniques in installation, the longevity and performance of the bullplugs are maximized, underscoring the importance of seasoned expertise in the oil and gas sector.
bullplugs
The authoritative voice of industry leaders often highlights innovation in bullplug technology.
Recent advancements have seen the incorporation of smart technology into bullplug designs. These innovations allow for real-time monitoring of pressure and temperature within the sealed sections, providing crucial data that can preemptively signal potential breaches or failures. Adopting these modernized tools reflects an authoritative commitment to enhancing safety measures and operational efficiency, positioning companies at the forefront of technological progression.
Trust is paramount when it comes to components used in oil and gas operations. The industry demands components that are not only effective but also reliable under extreme conditions. The track record of bullplugs in maintaining integrity and preventing accidents has cemented their status as trustworthy elements within operations. Manufacturers maintain stringent quality control processes, ensuring each bullplug meets the highest standards, further reinforcing their credibility and trustworthiness.
In conclusion, bullplugs represent an intersection of reliability, innovation, and environmental responsibility. Their efficacy in sealing and maintaining pipeline integrity is backed by extensive expertise and authoritative endorsements from seasoned professionals. As the industry continues to evolve, bullplugs are poised to remain a cornerstone of operational efficiency, safety, and sustainability, making them an essential component in the ever-evolving landscape of oil and gas operations.