Tubing and casing are integral components of the oil and gas industry, playing crucial roles in ensuring efficient resource extraction. This article delves into the significance of these components, their unique features, and why selecting the right tubing and casing is essential for optimizing drilling operations.
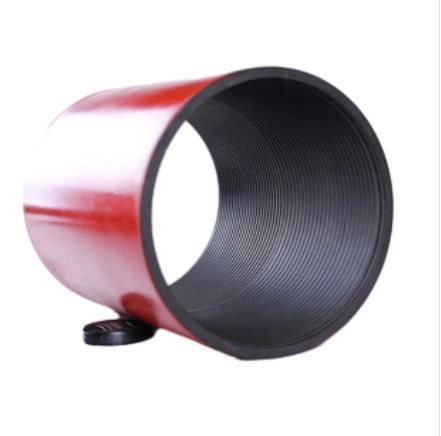
Understanding tubing and casing begins with recognizing their primary functions.
Tubing is the conduit through which oil and gas are transported from the reservoir to the surface. It needs to withstand high pressures and corrosive conditions while maintaining the structural integrity necessary for efficient flow. Casing, on the other hand, serves as a protective layer for the borehole, preventing collapse and uncontrollable pressure from surrounding formations. It is also crucial for isolating problematic layers within the earth, maintaining well integrity throughout the drilling and production processes.
An essential factor in the selection of tubing and casing is the material composition. Typically, these are crafted from high-grade steel or other metal alloys, chosen for their strength and resistance to corrosion. Recent innovations have introduced chromium-enhanced steels and other composite materials, designed to extend the lifespan of these components while reducing maintenance costs. The development and testing of these materials are underpinned by advancements in metallurgy and material sciences, proving their application even in offshore and ultra-deep drilling scenarios.
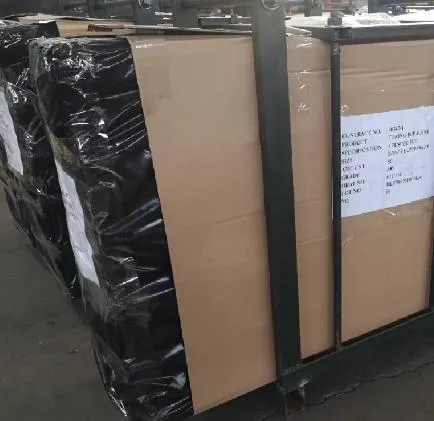
Moreover, the dimensions of tubing and casing, such as diameter and wall thickness, must be meticulously chosen based on the specific requirements of the drilling site. Incorrect sizing can lead to inefficiencies or even failures that could compromise an entire operation. In fact, selecting the appropriate size necessitates a deep understanding of the geological conditions and operational pressures of a given site, making this decision a highly specialized task for industry experts.
The installation of tubing and casing also offers unique challenges. Proper installation requires precision engineering to ensure that no component is subject to undue stress or misalignment. Companies increasingly rely on sophisticated computer modeling and simulation software to predict potential stress points and optimize installation processes before any physical work begins. These technologies help in mitigating risks and ensuring that the structures can handle various environmental stresses and operational demands.
tubing and casing
Furthermore, regular monitoring and maintenance are pivotal in prolonging the life and efficiency of tubing and casing. Advanced diagnostic tools, such as fiber optic sensors, are employed to detect early signs of wear or damage. By analyzing data gathered from these sensors, engineers can make informed decisions about preventative maintenance or necessary replacements, thus preventing costly downtimes.
Industry partnerships also play a significant role, enhancing the authority and credibility of companies within the tubing and casing sector. Collaborative research initiatives with academic and technical institutions allow companies to stay at the forefront of technological advancements and adhere to the highest standards of industry practice. This commitment to continued learning and improvement fosters an environment of trust and reliability among clients and stakeholders alike.
Notably, sustainability has become an increasingly important consideration in the production and selection of tubing and casing. With global emphasis on reducing carbon footprints, companies are innovating with new materials and processes that minimize environmental impact while maximizing resource efficiency. Green steel production, recycling programs, and more stringent regulations on emissions showcase a growing commitment to greener practices within the industry.
In conclusion, the strategic selection and effective management of tubing and casing are vital for optimizing oil and gas operations. Through the integration of advanced materials, cutting-edge technology, and sustainable practices, companies can enhance operational efficiency while maintaining safety and environmental responsibility. Whether onshore or offshore, these components form the backbone of any successful drilling operation, essential in meeting the world's energy demands securely and efficiently.