The bull plug, a vital component in various industrial sectors, particularly oil and gas, remains mysterious to many outside these industries. Its function centers around sealing or terminating connections in piping systems, playing a crucial role in maintaining operational integrity. Designed to withstand high pressure and harsh environments, bull plugs are indispensable in the construction and maintenance of pipelines and other essential infrastructure.
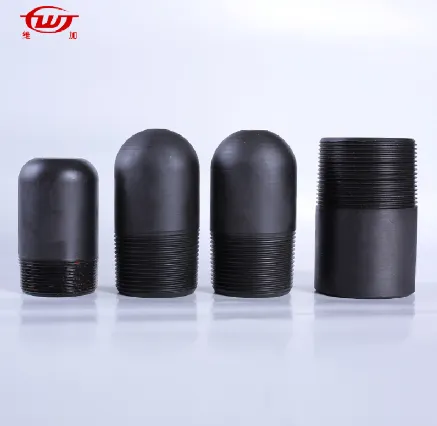
Manufactured from robust materials, usually carbon steel, stainless steel, or other alloys, bull plugs are engineered to endure the extreme conditions commonly found in industrial environments. These plugs are meticulously shaped, typically cylindrical, with features like threading or welding ends, allowing for secure attachments within piping systems. The ability of a bull plug to provide a perfect seal is paramount, ensuring no leakage occurs that could compromise system safety or efficiency.
From a technical standpoint, bull plugs are categorized based on size, material, pressure rating, and connection type.
Each of these elements is critical in choosing the right bull plug for a specific application. The size and threading need to match perfectly with the rest of the piping system, while the material and pressure rating need to align with the operational demands. For instance, in high-temperature environments, using a bull plug made of heat-resistant materials is essential, whereas in corrosive environments, stainless steel or specific alloys might be more appropriate.
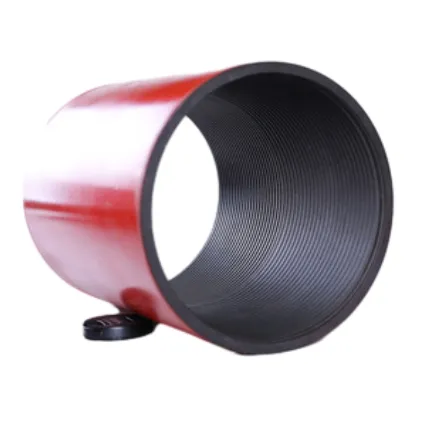
From an Experience perspective, seasoned engineers and technicians often highlight the importance of precise installation processes when dealing with bull plugs. Incorrect installation can lead to potential failures, which could result in leaks, environmental hazards, and costly downtimes. Thus, professionals emphasize the importance of adhering to manufacturer guidelines and industry standards during the installation process. Routine inspections and maintenance checks are also recommended to ensure the longevity and effectiveness of bull plugs.
what is bull plug
Expertise in the field further confirms the importance of choosing the right type of bull plug. Engineers often conduct rigorous assessments of their systems' requirements, evaluating aspects like fluid type, pressure levels, and environmental conditions, before selecting the ideal bull plug. The consultation with manufacturers or suppliers for tailored advice often forms part of this process, ensuring the bull plug's compatibility with specific industry needs.
Authoritativeness in the industry is demonstrated by manufacturers who provide comprehensive data sheets and certifications for their bull plugs. These documents serve as proof of quality and reliability, showcasing the bull plug's capabilities and compliance with industry standards. Top manufacturers invest in research and development to innovate and enhance the performance and resistance of their bull plugs, continually setting industry benchmarks.
Trustworthiness is cemented by a manufacturer's reputation and the longevity of their products. Companies known for their durable and reliable bull plugs often see repeat business, with their products trusted in critical settings where failure is not an option. Customer feedback and case studies highlighting long-term success stories with bull plug applications serve as powerful testimonials of a product's reliability.
In the journey of understanding bull plugs, from their fundamental role to the critical considerations for their use, it becomes evident that these components, while small, are mighty players in sustaining industrial safety and productivity. The right bull plug, chosen with attention to detail and installed with precision, can make a significant difference in an operation's overall success, ensuring systems function smoothly, safely, and efficiently in even the most demanding conditions.